§ 63.1257 Test methods and compliance procedures.
(a) General. Except as specified in paragraph (a)(5) of this section, the procedures specified in paragraphs (c), (d), (e), and (f) of this section are required to demonstrate initial compliance with §§ 63.1253, 63.1254, 63.1256, and 63.1252(e), respectively. The provisions in paragraphs (a)(2) and (3) apply to performance tests that are specified in paragraphs (c), (d), and (e) of this section. The provisions in paragraph (a)(5) of this section are used to demonstrate initial compliance with the alternative standards specified in §§ 63.1253(d) and 63.1254(c). The provisions in paragraph (a)(6) of this section are used to comply with the outlet concentration requirements specified in §§ 63.1253(c), 63.1254(a)(2)(i), and (a)(3)(ii)(B), 63.1254(b)(i), and 63.1256(h)(2). Performance tests shall be conducted under such conditions representative of performance of the affected source for the period being tested. Upon request, the owner or operator shall make available to the Administrator such records as may be necessary to determine the conditions of performance tests.
(1) Design evaluation. To demonstrate that a control device meets the required control efficiency, a design evaluation must address the composition and organic HAP concentration of the vent stream entering the control device. A design evaluation also must address other vent stream characteristics and control device operating parameters as specified in any one of paragraphs (a)(1) (i) through (vi) of this section, depending on the type of control device that is used. If the vent stream is not the only inlet to the control device, the efficiency demonstration also must consider all other vapors, gases, and liquids, other than fuels, received by the control device.
(i) For an enclosed combustion device used to comply with the provisions of 63.1253 (b)(2) or (c)(2), or 63.1256(h)(2)(i)(C) with a minimum residence time of 0.5 seconds and a minimum temperature of 760 °C, the design evaluation must document that these conditions exist.
(ii) For a combustion control device that does not satisfy the criteria in paragraph (a)(1)(i) of this section, the design evaluation must document control efficiency and address the following characteristics, depending on the type of control device:
(A) For a thermal vapor incinerator, the design evaluation must consider the autoignition temperature of the organic HAP, must consider the vent stream flow rate, and must establish the design minimum and average temperature in the combustion zone and the combustion zone residence time.
(B) For a catalytic vapor incinerator, the design evaluation shall consider the vent stream flow rate and shall establish the design minimum and average temperatures across the catalyst bed inlet and outlet.
(C) For a boiler or process heater, the design evaluation shall consider the vent stream flow rate; shall establish the design minimum and average flame zone temperatures and combustion zone residence time; and shall describe the method and location where the vent stream is introduced into the flame zone.
(iii) For a condenser, the design evaluation shall consider the vent stream flow rate, relative humidity, and temperature and shall establish the design outlet organic HAP compound concentration level, design average temperature of the condenser exhaust vent stream, and the design average temperatures of the coolant fluid at the condenser inlet and outlet. The temperature of the gas stream exiting the condenser must be measured and used to establish the outlet organic HAP concentration.
(iv) For a carbon adsorption system that regenerates the carbon bed directly onsite in the control device such as a fixed-bed adsorber, the design evaluation shall consider the vent stream flow rate, relative humidity, and temperature and shall establish the design exhaust vent stream organic compound concentration level, adsorption cycle time, number and capacity of carbon beds, type and working capacity of activated carbon used for carbon beds, design total regeneration stream mass or volumetric flow over the period of each complete carbon bed regeneration cycle, design carbon bed temperature after regeneration, design carbon bed regeneration time, and design service life of carbon. For vacuum desorption, the pressure drop shall be included.
(v) For a carbon adsorption system that does not regenerate the carbon bed directly onsite in the control device such as a carbon canister, the design evaluation shall consider the vent stream mass or volumetric flow rate, relative humidity, and temperature and shall establish the design exhaust vent stream organic compound concentration level, capacity of carbon bed, type and working capacity of activated carbon used for carbon bed, and design carbon replacement interval based on the total carbon working capacity of the control device and source operating schedule.
(vi) For a scrubber, the design evaluation shall consider the vent stream composition; constituent concentrations; liquid-to-vapor ratio; scrubbing liquid flow rate and concentration; temperature; and the reaction kinetics of the constituents with the scrubbing liquid. The design evaluation shall establish the design exhaust vent stream organic compound concentration level and will include the additional information in paragraphs (a)(1)(vi)(A) and (B) of this section for trays and a packed column scrubber.
(A) Type and total number of theoretical and actual trays;
(B) Type and total surface area of packing for entire column, and for individual packed sections if column contains more than one packed section.
(2) Calculation of TOC or total organic HAP concentration. The TOC concentration or total organic HAP concentration is the sum of the concentrations of the individual components. If compliance is being determined based on TOC, the owner or operator shall compute TOC for each run using Equation 6 of this subpart. If compliance with the wastewater provisions is being determined based on total organic HAP, the owner or operator shall compute total organic HAP using Equation 6 of this subpart, except that only the organic HAP compounds shall be summed; when determining compliance with paragraph (e)(3)(i) of this section, only the soluble and partially soluble HAP compounds shall be summed.

where:
(3) Outlet concentration correction for supplemental gases—(i) Combustion devices. Except as provided in § 63.1258(b)(5)(ii)(A), for a combustion device used to comply with an outlet concentration standard, the actual TOC, organic HAP, and hydrogen halide and halogen must be corrected to 3 percent oxygen if supplemental gases, as defined in § 63.1251, are added to the vent stream or manifold. The integrated sampling and analysis procedures of Method 3B of 40 CFR part 60, appendix A, shall be used to determine the actual oxygen concentration (%O2d). The samples shall be taken during the same time that the TOC or total organic HAP or hydrogen halides and halogen samples are taken. The concentration corrected to 3 percent oxygen (Cd) shall be computed using Equation 7A of this subpart:
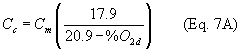
Where:
(ii) Noncombustion devices. Except as provided in § 63.1258(b)(5)(ii)(B), if a control device other than a combustion device is used to comply with a TOC, organic HAP, or hydrogen halide outlet concentration standard, the owner or operator must correct the actual concentration for supplemental gases using Equation 7B of this subpart; process knowledge and representative operating data may be used to determine the fraction of the total flow due to supplemental gas.
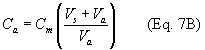
Where:
(4) Exemptions from compliance demonstrations. An owner or operator using any control device specified in paragraphs (a)(4)(i) through (iv) of this section is exempt from the initial compliance provisions in paragraphs (c), (d), and (e) of this section.
(i) A boiler or process heater with a design heat input capacity of 44 megawatts or greater.
(ii) A boiler or process heater into which the emission stream is introduced with the primary fuel.
(iii) A boiler or process heater burning hazardous waste for which the owner or operator:
(A) Has been issued a final permit under 40 CFR part 270 and complies with the requirements of 40 CFR part 266, subpart H, or
(B) Has certified compliance with the interim status requirements of 40 CFR part 266, subpart H.
(iv) A hazardous waste incinerator for which the owner or operator has been issued a final permit under 40 CFR part 270 and complies with the requirements of 40 CFR part 264, subpart O, or has certified compliance with the interim status requirements of 40 CFR part 265, subpart O.
(5) Initial compliance with alternative standard. Initial compliance with the alternative standards in §§ 63.1253(d) and 63.1254(c) for combustion devices is demonstrated when the outlet TOC concentration is 20 ppmv or less, and the outlet hydrogen halide and halogen concentration is 20 ppmv or less. Initial compliance with the alternative standards in §§ 63.1253(d) and 63.1254(c) for noncombustion devices is demonstrated when the outlet TOC concentration is 50 ppmv or less, and the outlet hydrogen halide and hydrogen concentration is 50 ppmv or less. To demonstrate initial compliance, the owner or operator shall be in compliance with the monitoring provisions in § 63.1258(b)(5) on the initial compliance date. The owner or operator shall use Method 18 to determine the predominant organic HAP in the emission stream if the TOC monitor is calibrated on the predominant HAP.
(6) Initial compliance with the 20 ppmv outlet limit. Initial compliance with the 20 ppmv TOC and hydrogen halide and halogen concentration is demonstrated when the outlet TOC concentration is 20 ppmv or less, and the outlet hydrogen halide and halogen concentration is 20 ppmv or less. To demonstrate initial compliance, the operator shall use test methods described in paragraph (b) of this section. The owner or operator shall comply with the monitoring provisions in § 63.1258(b)(1) through (4) on the initial compliance date.
(b) Test methods. When testing is conducted to measure emissions from an affected source, the test methods specified in paragraphs (b)(1) through (10) of this section shall be used.
(1) EPA Method 1 or 1A of appendix A of part 60 is used for sample and velocity traverses.
(2) EPA Method 2, 2A, 2C, or 2D of appendix A of part 60 is used for velocity and volumetric flow rates.
(3) EPA Method 3 of appendix A of part 60 is used for gas analysis.
(4) EPA Method 4 of appendix A of part 60 is used for stack gas moisture.
(5) [Reserved]
(6) The following methods are specified for concentration measurements:
(i) Method 18 may be used to determine HAP concentration in any control device efficiency determination.
(ii) Method 25 of appendix A of part 60 may be used to determine total gaseous nonmethane organic concentration for control efficiency determinations in combustion devices.
(iii) Method 26 or 26A of appendix A of part 60 shall be used to determine hydrogen chloride, hydrogen halide and halogen concentrations in control device efficiency determinations or in the 20 ppmv outlet hydrogen halide concentration standard.
(iv) Method 25A of appendix A of part 60 may be used to determine the HAP or TOC concentration for control device efficiency determinations under the conditions specified in Method 25 of appendix A for direct measurement of an effluent with a flame ionization detector, or in demonstrating compliance with the 20 ppmv TOC outlet standard. If Method 25A is used to determine the concentration of TOC for the 20 ppmv standard, the instrument shall be calibrated on methane or the predominant HAP. If calibrating on the predominant HAP, the use of Method 25A shall comply with paragraphs (b)(6)(iv)(A) through (C) of this section.
(A) The organic HAP used as the calibration gas for Method 25A, 40 CFR part 60, appendix A, shall be the single organic HAP representing the largest percent by volume.
(B) The use of Method 25A, 40 CFR part 60, appendix A, is acceptable if the response from the high level calibration gas is at least 20 times the standard deviation of the response from the zero calibration gas when the instrument is zeroed on the most sensitive scale.
(C) The span value of the analyzer must be less than 100 ppmv.
(7) Testing conditions for continuous processes. Testing of emissions on equipment operating as part of a continuous process will consist of three l-hour runs. Gas stream volumetric flow rates shall be measured every 15 minutes during each 1-hour run. The HAP concentration shall be determined from samples collected in an integrated sample over the duration of each l-hour test run, or from grab samples collected simultaneously with the flow rate measurements (every 15 minutes). If an integrated sample is collected for laboratory analysis, the sampling rate shall be adjusted proportionally to reflect variations in flow rate. For continuous gas streams, the emission rate used to determine compliance shall be the average emission rate of the three test runs.
(8) Testing and compliance determination conditions for batch processes. Testing of emissions on equipment where the flow of gaseous emissions is intermittent (batch operations) shall be conducted as specified in paragraphs (b)(8)(i) through (iii) of this section.
(i) Except as provided in paragraph (b)(9) of this section for condensers, testing shall be conducted at absolute worst-case conditions or hypothetical worst-case conditions. Gas stream volumetric flow rates shall be measured at 15-minute intervals. The HAP or TOC concentration shall be determined from samples collected in an integrated sample over the duration of the test, or from grab samples collected simultaneously with the flow rate measurements (every 15 minutes). If an integrated sample is collected for laboratory analysis, the sampling rate shall be adjusted proportionally to reflect variations in flow rate. The absolute worst-case or hypothetical worst-case conditions shall be characterized by the criteria presented in paragraphs (b)(8)(i)(A) and (B)of this section. In all cases, a site-specific plan shall be submitted to the Administrator for approval prior to testing in accordance with § 63.7(c) and § 63.1260(l). The test plan shall include the emission profile described in paragraph (b)(8)(ii) of this section.
(A) Absolute worst-case conditions are defined by the criteria presented in paragraph (b)(8)(i)(A)(1) or (2) of this section if the maximum load is the most challenging condition for the control device. Otherwise, absolute worst-case conditions are defined by the conditions in paragraph (b)(8)(i)(A)(3) of this section. The owner or operator must consider all relevant factors, including load and compound-specific characteristics in defining absolute worst-case conditions.
(1) The period in which the inlet to the control device will contain at least 50 percent of the maximum HAP load (in lb) capable of being vented to the control device over any 8 hour period. An emission profile as described in paragraph (b)(8)(ii)(A) of this section shall be used to identify the 8-hour period that includes the maximum projected HAP load.
(2) A 1-hour period of time in which the inlet to the control device will contain the highest HAP mass loading rate, in lb/hr, capable of being vented to the control device. An emission profile as described in paragraph (b)(8)(ii)(A) of this section shall be used to identify the 1-hour period of maximum HAP loading.
(3) The period of time when the HAP loading or stream composition (including non-HAP) is most challenging for the control device. These conditions include, but are not limited to the following:
(i) Periods when the stream contains the highest combined VOC and HAP load, in lb/hr, described by the emission profiles in paragraph (b)(8)(ii) of this section;
(ii) Periods when the streams contain HAP constituents that approach limits of solubility for scrubbing media;
(iii) Periods when the streams contain HAP constituents that approach limits of adsorptivity for carbon adsorption systems.
(B) Hypothetical worst-case conditions are simulated test conditions that, at a minimum, contain the highest hourly HAP load of emissions that would be predicted to be vented to the control device from the emissions profile described in paragraph (b)(8)(ii)(B) or (C) of this section.
(ii) Emissions profile. The owner or operator may choose to perform tests only during those periods of the worst-case conditions that the owner or operator selects to control as part of achieving the required emission reduction. The owner or operator must develop an emission profile for the vent to the control device that describes the characteristics of the vent stream at the inlet to the control device under worst case conditions. The emission profile shall be developed based on any one of the procedures described in (b)(8)(ii)(A) through (C) of this section, as required by paragraph (b)(8)(i).
(A) Emission profile by process. The emission profile must consider all emission episodes that could contribute to the vent stack for a period of time that is sufficient to include all processes venting to the stack and shall consider production scheduling. The profile shall describe the HAP load to the device that equals the highest sum of emissions from the episodes that can vent to the control device in any given hour. Emissions per episode shall be calculated using the procedures specified in paragraph (d)(2) of this section. Emissions per episode shall be divided by the duration of the episode only if the duration of the episode is longer than 1 hour.
(B) Emission profile by equipment. The emission profile must consist of emissions that meet or exceed the highest emissions, in lb/hr, that would be expected under actual processing conditions. The profile shall describe equipment configurations used to generate the emission events, volatility of materials processed in the equipment, and the rationale used to identify and characterize the emission events. The emissions may be based on using a compound more volatile than compounds actually used in the process(es), and the emissions may be generated from all equipment in the process(es) or only selected equipment.
(C) Emission profile by capture and control device limitation. The emission profile shall consider the capture and control system limitations and the highest emissions, in lb/hr, that can be routed to the control device, based on maximum flowrate and concentrations possible because of limitations on conveyance and control equipment (e.g., fans, LEL alarms and safety bypasses).
(iii) Three runs, at a minimum of 1 hour each and a maximum of 8 hours each, are required for performance testing. Each run must occur over the same worst-case conditions, as defined in paragraph (b)(8)(i) of this section.
(9) Testing requirements for condensers. For emission streams controlled using condensers, continuous direct measurement of condenser outlet gas temperature to be used in determining concentrations per the design evaluation described in § 63.1257(a)(1)(iii) is required.
(10) Wastewater testing. Wastewater analysis shall be conducted in accordance with paragraph (b)(10)(i), (ii), (iii), (iv), or (v) of this section.
(i) Method 305. Use procedures specified in Method 305 of 40 CFR part 63, appendix A, and comply with requirements specified in paragraph (b)(10)(vi) of this section.
(ii) EPA Method 624, 625, 1624, 1625, 1666, or 1671. Use procedures specified in EPA Method 624, 625, 1624, 1625, 1666, or 1671 of 40 CFR part 136, appendix A, and comply with requirements in paragraph (b)(10)(vi) of this section.
(iii) Method 8260 or 8270. Use procedures specified in Method 8260 or 8270 in “Test Methods for Evaluating Solid Waste, Physical/Chemical Methods,” EPA Publication No. SW–846, Third Edition, September 1986, as amended by Update I, November 15, 1992. As an alternative, an owner or operator may use any more recent, updated version of Method 8260 or 8270 approved by the EPA. For the purpose of using Method 8260 or 8270 to comply with this subpart, the owner or operator must maintain a formal quality assurance program consistent with either Section 8 of Method 8260 or Method 8270, and this program must include the following elements related to measuring the concentrations of volatile compounds:
(A) Documentation of site-specific procedures to minimize the loss of compounds due to volatilization, biodegradation, reaction, or sorption during the sample collection, storage, and preparation steps.
(B) Documentation of specific quality assurance procedures followed during sampling, sample preparation, sample introduction, and analysis.
(C) Measurement of the average accuracy and precision of the specific procedures, including field duplicates and field spiking of the material source before or during sampling with compounds having similar chemical characteristics to the target analytes.
(iv) Other EPA methods. Use procedures specified in the method, validate the method using the procedures in paragraph (b)(10)(iv)(A) or (B) of this section, and comply with the procedures in paragraph (b)(10)(vi) of this section.
(A) Validate the method according to section 5.1 or 5.3 of Method 301 of 40 CFR part 63, appendix A.